SMT Manufacturing Process And Capability
The abbreviation for Surface Mount Technology, SMT is a surface mounting technology. This electronic assembly technology originated in the 1960s, and was initially developed by the U.S. IBM, and further matured during the late 1980s. Through this technology, electronic components such as resistors, capacitors, transistors and integrated circuits are mounted on printed circuit boards and lead soldered to form electric coupling. Components used in this process are called SMD (surface-mount devices). The greatest difference between SMT and through-hole technology is that SMT does not require corresponding holes to be reserved for component pins, and hence the sizes of SMD are much smaller than the sizes of components used in through-hole technology. This SMT technology for greatly reducing the size of electronic products and creating lightweight and slim products is briefly referred to as the SMT process. HIPO has a long-standing cooperation with domestic and foreign electronic products manufacturers. Its accumulated wealth of professional experience in SMT OEM has repeatedly won excellent domestic and international evaluation and recognition in the SMT OEM industry for electronics manufacturing.
HIPO has five fully automatic high-speed Panasonic equipment nitrogen furnace SMT production line that can produce a daily maximum of 5, K, K point components.
Minimum: 01005 Chip Component
Maximum: L150mm*W55mm*T25mm
Board Size:
Minimum L50mm*W50mm ~
Maximum L510mm*W460mm
Auxiliary Production Equipment
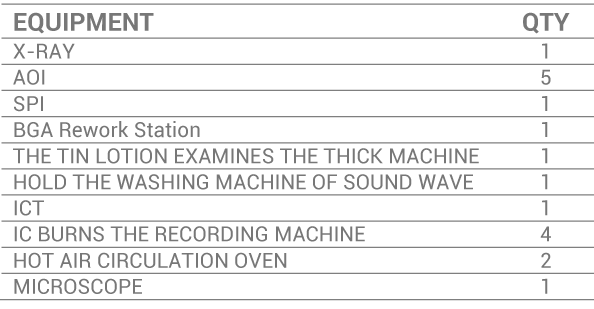
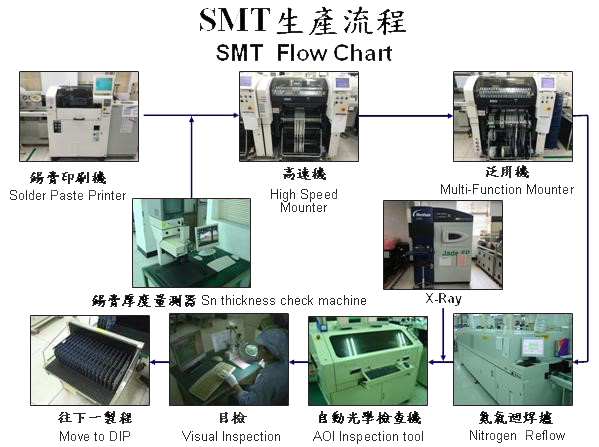
DIP Manufacturing Process And Capability
The abbreviation for Dual In Line Package Process, DIP is a dual-line packing for component installation. It is an integration of traditional electronic component and PCB processing. Modern electronic products are expected to be lightweight, slim and compact, and hence most DIP components have been replaced by SMD. DIP soldering is different from SMT process. Briefly, this is a technology where components are manually inserted into PCB holes (PTH), and using Flux sprayer, an appropriate amount of flux is sprayed onto the back of the PCB. Then after preheating and dipping in the tin furnace, the liquid tin adheres to the component pins and PCB holes to attach the electronic components to the PCB-PAD, thereby completing the assembly and mounting process, which is briefly referred to as DIP manufacturing process.
HIPO has two insertion, touch-up, and hand soldering lines and non-lead furnace DIP production lines, and together with devices such as thermostat soldering pens and dispensers, up to L400mm * W400mm sized PCB can be produced.
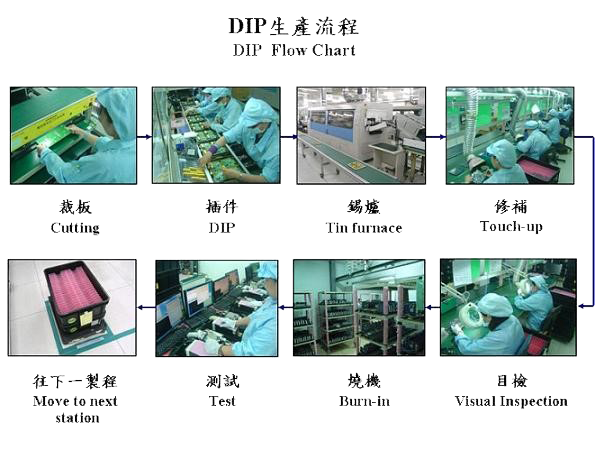
Finished Product Testing, Assembly Process and Capability
Assembly testing process (also called integration testing or the joint test) is a logical extension of unit testing. Its simplest form comprises combining two tested units into a component, and then testing their interface. In this sense, a component is defined as the integration of many units.
In actual practice, many elements are combined into a unit, and these components are then aggregated to become a larger component of a program. The process involves testing component parts, and then extending the process to test your module together with other modules, and finally testing all the modules that are assembled together in the process. In addition, if the program comprises multiple processes, then the processes are tested in pairs rather than tested simultaneously, and this testing process is briefly referred to as the assembly testing process.
HIPO has three finished product assembly lines, and according to customer need in manufacturing process, there are 80 test stations with different function tests to deliver strict quality checks.
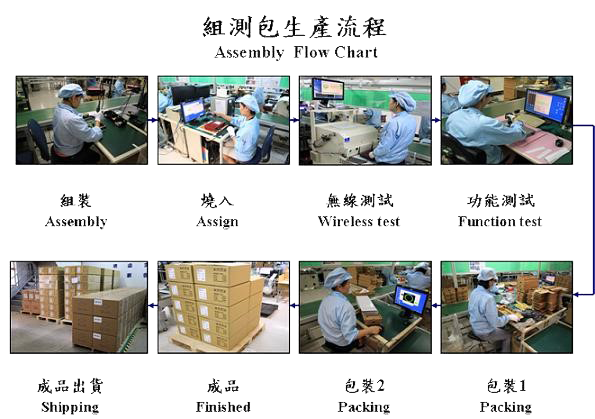